Industrial valves emerged after the invention of the steam engine. In the past twenty to thirty years, due to the demands of industries such as petroleum, chemicals, power stations, metallurgy, shipbuilding, nuclear energy, and aerospace, higher requirements have been placed on valves, prompting the research and production of high-parameter valves.
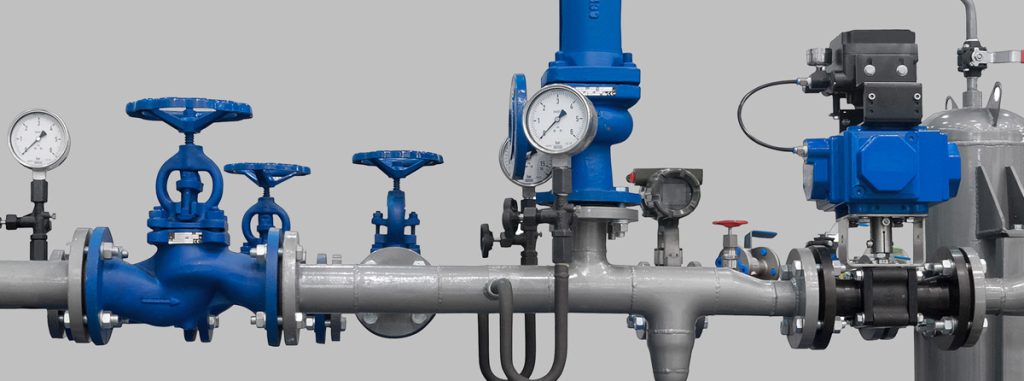
Their operating temperatures range from ultra-low temperatures of -269℃ to high temperatures of 1200°C, and even up to 3430℃. Working pressures vary from ultra-vacuum conditions of 1.33×10-10 mmHg) to ultra-high pressures of 1460 MPa. Valve diameters range from 1 mm to 6000 mm, and can even reach 9750 mm. The materials used for valves have evolved from cast iron and carbon steel to titanium and titanium alloy steel, as well as high-strength corrosion-resistant steel, cryogenic steel, and heat-resistant steel valves. The actuation methods for valves have also advanced, from manual operation to electric, pneumatic, hydraulic, and even programmed control, numerical control, and remote control. The processing technology for valves has also transitioned from conventional machine tools to assembly lines and automated lines.
There are many classification methods for valves based on their different functions in opening and closing. Here are several classifications introduced below.
1. Classification of Industrial Valves
1.1 Classification by Function and Purpose
(1) Stop Valves: Stop valves, also known as blocking valves, connect or disconnect the medium in the pipeline. This category includes gate valves, globe valves, plug valves, ball valves, butterfly valves, and diaphragm valves.
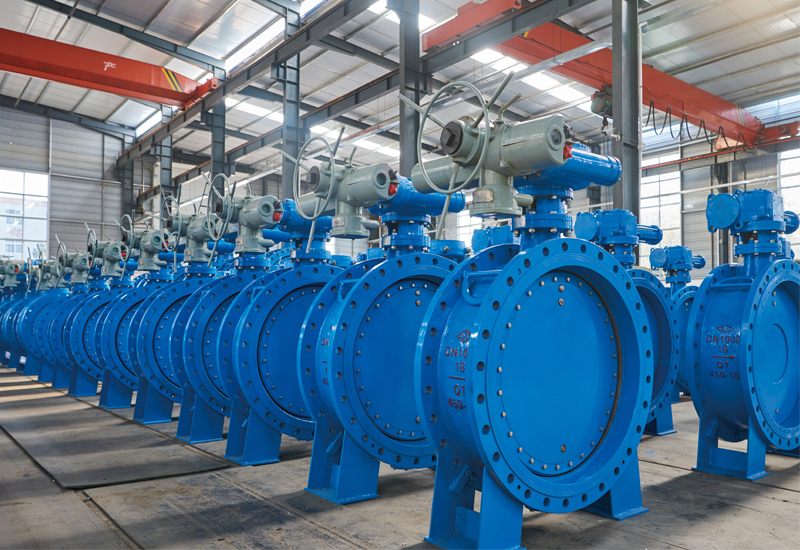
(2) Check Valves: Check valves, also known as non-return valves or one-way valves, prevent the medium in the pipeline from flowing backward. The bottom valve of a water pump suction also belongs to this category.
(3) Safety Valves: Safety valves are designed to prevent the pressure of the medium in the pipeline or device from exceeding the specified value, thereby achieving the purpose of safety protection.
(4) Control Valves: Control valves, including control valves, throttle valves, and pressure reducing valves, are used to regulate the pressure, flow rate, and other parameters of the medium.
(5) Diverting Valves: Diverting valves, including various distribution valves and trap valves, are used to distribute, separate, or mix the medium in the pipeline.
1.2 Classification by Nominal Pressure
(1) Vacuum Valves: Valves with a working pressure lower than standard atmospheric pressure.
(2) Low-Pressure Valves: Valves with a nominal pressure PN of ≤1.6 MPa.
(3) Medium-Pressure Valves: Valves with a nominal pressure PN of 2.5, 4.0, or 6.4 MPa.
(4) High-Pressure Valves: Valves with a nominal pressure PN ranging from 10 to 80 MPa.
(5) Ultra-High-Pressure Valves: Valves with a nominal pressure PN of ≥100 MPa.
1.3 Classification by Operating Temperature
(1) Cryogenic Valves: Valves used for media with an operating temperature of t < -100℃.
(2) Low-Temperature Valves: Valves used for media with an operating temperature range of -100℃≤ t ≤ -40℃.
(3) Normal-Temperature Valves: Valves used for media with an operating temperature range of -40℃≤ t ≤ 120℃
2. Application of Industrial Valves
With the various needs of modern life, the production of parts and components for these important products is also endless. Below, we list the main application fields of these ten categories of valves.
2.1 Valves for Petroleum Installations
Refining installations primarily require pipeline valves, including gate valves, globe valves, check valves, safety valves, ball valves, butterfly valves, and steam traps. Among them, gate valves account for about 80% of the total valve demand (valves account for 3% to 5% of the total investment in the installation).
Chemical fiber installations produce polyester, acrylic fiber, and vinylon. They mainly require ball valves and jacket valves (jacket ball valves, jacket gate valves, jacket globe valves).
Acrylonitrile installations generally require standard valves, such as gate valves, globe valves, check valves, ball valves, steam traps, needle globe valves, and plug valves. Among them, gate valves account for about 75% of the total valve demand.
Ammonia synthesis installations require different technical specifications for valves due to different ammonia synthesis raw materials and purification methods. Currently, domestic ammonia synthesis installations primarily require gate valves, globe valves, check valves, steam traps, butterfly valves, ball valves, diaphragm valves, control valves, needle valves, safety valves, and high-temperature, and low-temperature valves.
2.2 Valves for Hydro power Stations
As the construction of power stations in China is developing towards larger scales, large-diameter and high-pressure safety valves, pressure-reducing valves, globe valves, gate valves, butterfly valves, emergency shut-off valves, and flow control valves, as well as spherical-sealed instrument globe valves, are required. (According to the national "Fifteenth Five-Year Plan," except for Inner Mongolia and Guizhou, which can still build units with a capacity of more than 200,000 kW, other provinces and cities can only build units with a capacity of more than 300,000 kW.)
2.3 Valves for Metallurgical Applications
In the metallurgical industry, alumina production mainly requires wear-resistant slurry valves (flow-type globe valves) and regulating steam traps. The steel-making industry mainly requires metal-sealed ball valves, butterfly valves, oxidized ball valves, globe flash valves, and four-way reversing valves.
2.4 Valves for Marine Applications
With the development of offshore oilfield exploitation, the demand for valves in marine platforms is gradually increasing. Marine platforms require shut-off ball valves, check valves, and multi-way valves.
2.5 Valves for Food and Pharmaceutical Applications
This industry primarily requires stainless steel ball valves, non-toxic full-plastic ball valves, and butterfly valves. Among the above ten categories of valve products, the demand for general-purpose valves is relatively high, such as instrument valves, needle valves, needle globe valves, gate valves, globe valves, check valves, ball valves, and butterfly valves.
2.6 Valves for Rural and Urban Construction
Urban construction systems generally use low-pressure valves and are currently developing towards environmental protection and energy-saving. Environmentally friendly rubber plate valves, balancing valves, and (central-line butterfly valves), as well as metal-sealed butterfly valves, are gradually replacing low-pressure iron gate valves. Domestic urban construction primarily requires balancing valves, soft-sealed gate valves, and butterfly valves.
2.7 Valves for Rural and Urban Heating
Urban heating systems require a large number of metal-sealed butterfly valves, horizontal balancing valves, and directly buried ball valves. These valves address vertical and horizontal hydraulic imbalances in pipelines, achieving energy-saving and heating balance objectives.
2.8 Valves for Environmental Protection Applications
In domestic environmental protection systems, water supply systems primarily require central-line butterfly valves, soft-sealed gate valves, ball valves, and air release valves (used to remove air from pipelines). Wastewater treatment systems primarily require soft-sealed gate valves and butterfly valves.
2.9 Valves for Gas Applications
Urban gas accounts for 22% of the entire natural gas market, with a large demand for valves and various types. Primarily required are ball valves, plug valves, pressure reducing valves, and safety valves.
2.10 Valves for Pipeline Applications
Long-distance pipelines primarily transport crude oil, refined oil, and natural gas. These pipelines primarily require forged steel three-body full-bore ball valves, sulfur-resistant plate gate valves, safety valves, and check valves.